Soaring Temperatures in India Necessitate Sustainable Cold Storage
CLASP visits cold chain sites across India to understand the ecosystem, rising challenges and potential avenues to increase efficiency.
On the outskirts of Delhi, CLASP visited two cold storage facilities to learn how policy can improve cold chain infrastructure across India. We are partnering with Alliance for an Energy Efficient Economy (AEEE) to support more resilient food chains in the face of increasingly severe weather.
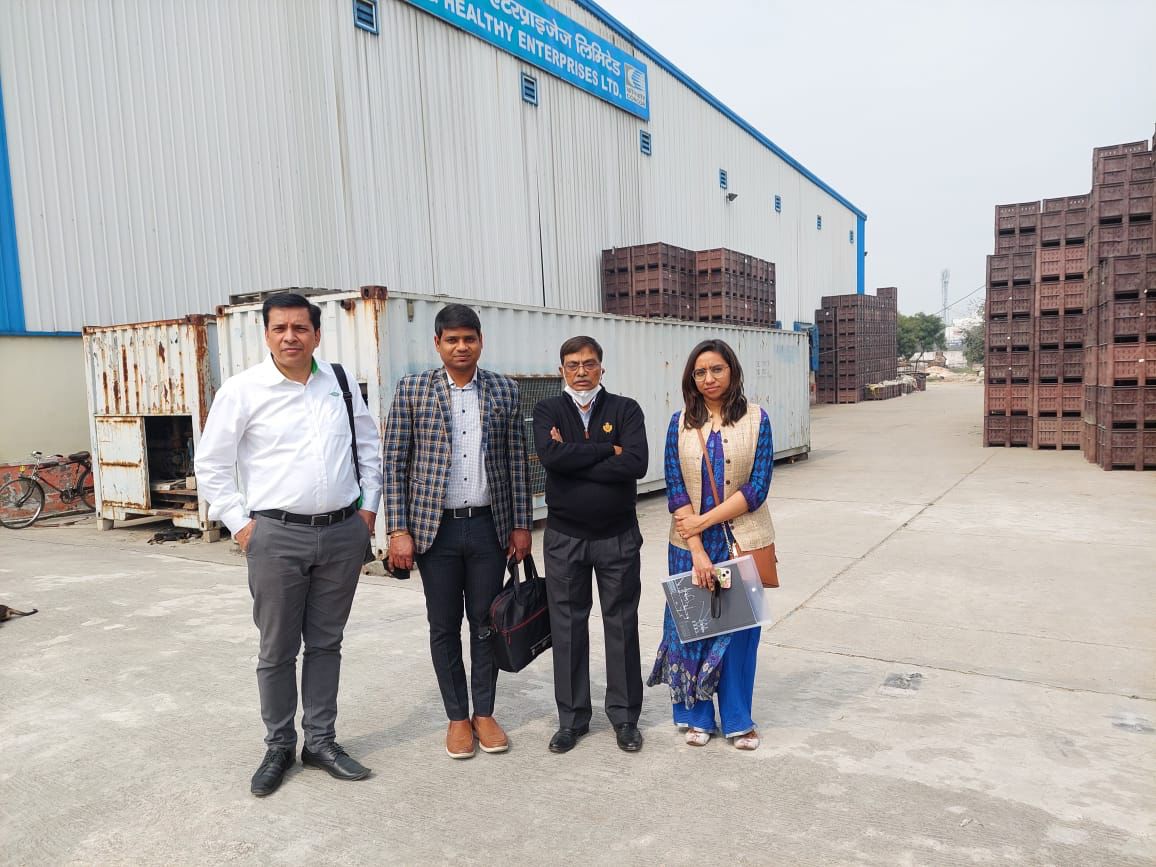
Rising Temperatures Put Crops at Risk
CLASP visited two cold chain units – ASPAM Cold Storage and Fresh Healthy Enterprise Limited (FHEL). Meeting with these companies offered important insights into the use cases and challenges we could address through better efficiency policies – namely lowering soaring electricity costs and increasing capacity for storage.
The FHEL unit sits in a remote midpoint for several neighboring cities. FHEL is one of several key actors in the regional cold chain, connecting farmers and agricultural cooperatives to larger businesses. With soaring temperatures across India and erratic rainfall, storage of produce is becoming an increasingly important aspect of food security efforts.
The local government has stepped in to support food chain infrastructure in Sonipat. The government allocated ASPAM Cold Food Storage land to build a cold storage unit and granted the company a 40% subsidy to fully automate the facility. The facility contains twenty-one Controlled Atmosphere (CA) chambers – highly effective technology to control the temperature and humidity. The combined capacity of this facility is 8500 MT (approximately the weight of 2236 full-sized shipping containers) and frozen storage capacity of 1500 MT.
Regulating Cold Rooms Requires Intensive Electricity
The ASPAM cold units require intensive electricity to maintain advanced temperate controlled rooms. The units maintain low levels of oxygen and high levels of carbon dioxide in gas-tight containers to retain freshness and nutritional content of fruits like apples and kiwis, as well as frozen produce like peas. The chambers employ unique storage protocols that vary depending on the product’s needs. For example, apples and kiwis are stored at 1-20°C, whereas dates and oranges are stored at 4-5°C. For reference, July temperatures in Sonipat average 28-39°C. Without the unit, the fruits would quickly rot.
The controlled atmosphere extends the shelf life of produce and reduces the need for post-harvest chemicals, usually sprayed for protection against insects and microorganisms. The unit also hosts a ripening chamber for fruits like bananas, mangoes and papayas. This is typically a 5-day cycle and requires a consistent temperature of 2°C and relative humidity of 95%. All the conditions in the cold rooms are controlled and monitored through a remote monitoring system.
The total cost to run these units is approximately INR 700,000 ($8778 USD) per month.
Power cuts are frequent in the area so ASPAM relies on a diesel generator for power backup.
Currently, CLASP is visiting cold storage facilities across the country to understand the ecosystem and the different requirements of cold chain infrastructure amidst varied weathers. CLASP aims to use this information to devise standards and labels for key cold chain equipment in the months to come.
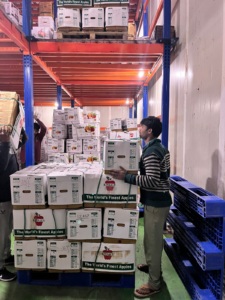
How can cold storage employ more design and technology innovations?
The unit maintains the variable temperatures efficiently by employing freon refrigeration technology. Freon is a non-combustible gas, typically used as a refrigerant in air cooling applications. By undergoing an evaporation process repeatedly, freon helps produce cool air that can be circulated throughout a unit. CLASP is standardizing the equipment that utilizes freon – ensuring that the gas is efficiently used in cold storage applications.
With the lessons learned from the visit to Sonipat and six other sites across India, our team will collaborate with industry leaders to achieve our goals. By 2030, our cold storage policies aim to mitigate 8.5 Mt of CO₂ emissions by adoption of high-efficiency agricultural cold chain solutions.
Learn more about how CLASP is contributing to more resilient cold chain systems around the world:
- CLASP celebrates and encourages innovation the cold chain sector – 2022 Global LEAP Awards Off-Grid Cold Chain Challenge Announces Preliminary Finalists
- Standards and Labeling Policy for Deep Freezers in India
- How a Solar-Powered Walk-In Cold Room is Cutting Post-Slaughter Losses for Butchers in Kenya